Achieving the Shortest Turnaround Time: Veeyor Polymers’ Success Story!
- July 15, 2024
- Posted by: veeyor@dmin
- Category: Uncategorized
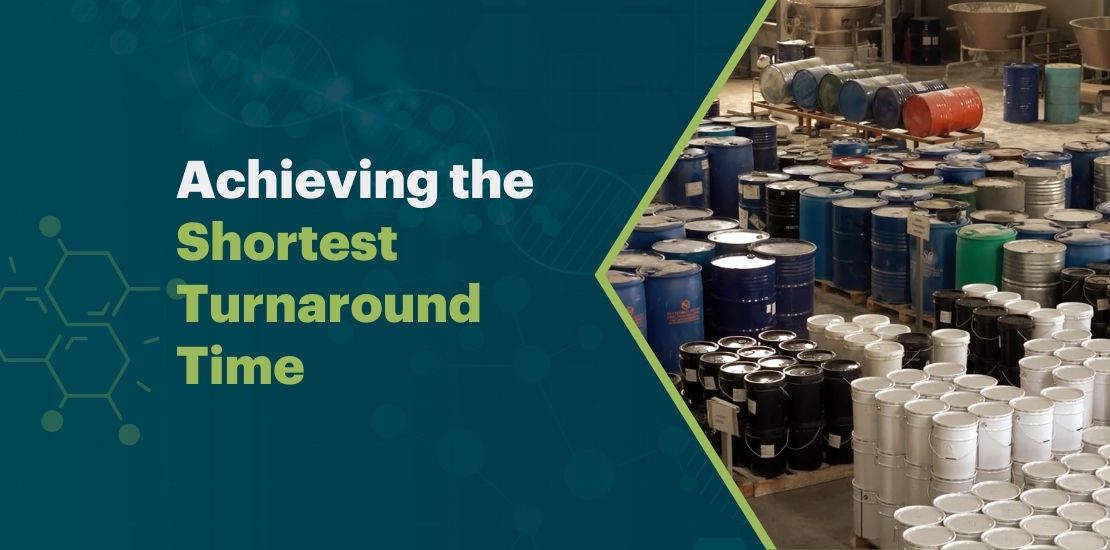
In Polymer manufacturing, efficiency is not just an advantage—it’s a necessity. Veeyor Polymers recently showcased an impressive feat: achieving the shortest turnaround time for their latest project. This success story is a testament to their strategic planning, effective teamwork, and adaptability.
The Challenge
Veeyor Polymers faced a significant challenge: reducing the turnaround time for a major project without compromising on quality. The goal was clear but was demanding meticulous planning and flawless execution.
Strategic Planning
The first step in their journey was thorough planning. The team at Veeyor Polymers began by setting clear objectives and identifying potential obstacles. They conducted brainstorming sessions to map out their approach, ensuring every team member understood their role and responsibilities. By leveraging the strengths of each member, they laid a solid foundation for the project’s success.
Streamlined Workflow
With a plan in place, the team moved to the implementation phase. They adopted a streamlined workflow designed to maximize efficiency and minimize delays. Key strategies included:
- Effective Communication: Keeping all team members informed about progress and potential issues.
- Task Prioritization: Focusing on critical tasks first to ensure timely completion.
- Resource Allocation: Ensuring that the necessary resources were available when needed.
These strategies helped the team maintain a steady pace and avoid common pitfalls that can delay projects.
Iterative Review and Adjustment:
One of the standout practices at Veeyor Polymers was their commitment to continuous improvement. Throughout the project, they regularly paused to review their progress. This allowed them to identify any bottlenecks or inefficiencies and make necessary adjustments promptly. This iterative process was crucial in maintaining momentum and ensuring the project stayed on track.
The Result:
Thanks to their meticulous planning, streamlined workflow, and iterative improvements, Veeyor Polymers achieved their goal. The project was completed in record time, setting a new benchmark for turnaround times in the industry. This accomplishment was not just about speed; it was also about maintaining high standards of quality and efficiency.
Lessons Learned
Veeyor Polymers’ success story offers valuable lessons for any organization looking to improve their efficiency:
- Plan Thoroughly: A clear, detailed plan is the foundation of any successful project.
- Communicate Effectively: Keeping everyone informed and involved is key to maintaining progress.
- Be Adaptable: Regular reviews and adjustments can help overcome obstacles and improve workflows.
- Leverage Team Strengths: Utilize the unique skills and strengths of each team member to drive success.