Choosing the Right PU based Adhesives for Filters: Key Factors to Boost Performance and Durability
- October 14, 2024
- Posted by: veeyor@dmin
- Category: Uncategorized
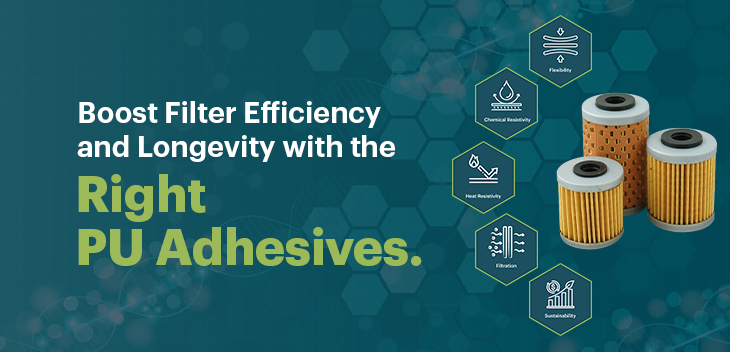
When selecting the right materials for filters, manufacturers must pay close attention to the properties of polyurethane (PU) Adhesives to ensure their filters meet both performance and durability standards. PU adhesive is a popular choice due to its versatility, but its effectiveness depends heavily on making the right selection.
Here are five key factors filter manufacturers should be aware of when choosing PU-Based Adhesives materials:
1. Get the Best Flow and Filtration
The primary function of any filter is to remove contaminants while allowing clean air or fluid to pass through. PU materials used in filters must support this by providing excellent porosity and permeability. Filters must allow optimal airflow or liquid flow without compromising on particle retention. The balance between filtration efficiency and permeability can directly impact the performance of the filter in applications like air filtration, automotive, or industrial systems.
2. Stay Strong Against Chemicals
Filters are often exposed to a variety of chemicals, oils, and solvents, especially in industries like automotive, manufacturing, and chemical processing. PU adhesive must be resistant to these substances to prevent degradation over time. Poor chemical resistance can lead to swelling, cracking, or even failure of the filter. Ensuring the PU material is chemically stable under these conditions will improve the filter’s lifespan and reliability.
3. Handle the Heat with Ease
4. Last Longer and Stay Flexible
5. Reduce ecological footprint
Veeyor Polymers specializes in providing advanced adhesive solutions that enhance the performance of filtration systems across industries. At Filtech Expo 2024, Veeyor will showcase its adhesives, formulated for high efficiency, durability, and compatibility with a wide range of filtration applications. Visit Veeyor Polymers at the event to discover how their adhesive innovations are helping filtration manufacturers build stronger, more reliable systems.